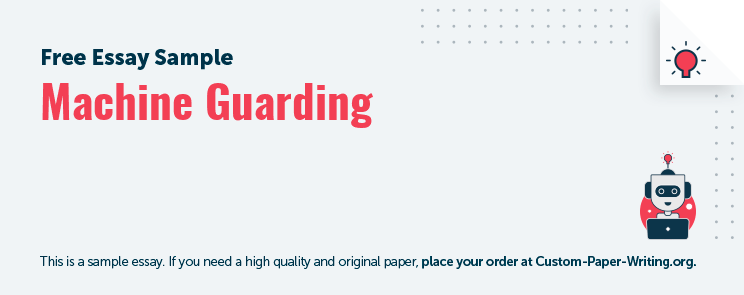
Machine Guarding Risk Assessment
Machine guarding risk assessment refers to the process that allows organizations to determine the intended use of a given machine, the hazards, and the level of risks associated with that machine. The implication of this statement is that the value of the machine guarding and risk assessment cannot be realized until an organization dedicates itself to reduce the identified risks to an acceptable level. An acceptable risk or a tolerable risk, according to ANS B11.0-2010 standards, refers to a level of risk at which further reduction in hazards cannot lead to significant reduction in risk. It involves a level of risk where additional resources and expenditures would not lead to significant advantages of the increased safety. The formats and requirements for conducting a machine guarding risk assessments are flexible; several sizes may be employed.
The Process of Machine Guarding Risk Assessment
According to Roudebush (2005), the process of the machine guarding risk assessment can be divided into five primary procedural steps. Those are gathering the equipment or device specification or information, determining the equipment limitation, identifying the machine and risk hazards, estimating risk, and determining the level of tolerable risk.
Calculate the cost of essay
Gathering Machine Information or Specifications
At the beginning of the machine guarding risk assessment, the one must collect historical data concerning the machine. Typically, the specified information and data required for conducting a risk evaluation process include technical drawing, system description, system layout diagrams, energy sources data, incident or accident history, and future expansion integration. The risk assessor should start by compiling a list of all the machines he or she would assess for risks (Roudebush, 2005). The assessor may consider machines as a single unit in situations where they are linked together either through conventional machine control systems or mechanically. For quantitative analysis purposes, the one may decide to correlating hazard historical data with machines of similar status and caliber that may provide the parameters for determining the levels of risks. The assessor may obtain such information from database summaries of state worker compensation by visiting a state website. In situations where the appraiser cannot get the necessary information online, he or she may decide to directly contact the state worker bureau. The implication is that an assessor should not over rely on the historical data from an organization’s loss experience because the data may not show the real level of risk.
Limited time Offer
with code
Determining Equipment Limitation
Before proceeding with the process of machine guarding risk assessment, the one must evaluate five major machine limitation areas. The first area is the use limitation which can be determined when the risk assessor evaluates the intended use of given equipment including its rates of production, operation speed, cycle times, materials used, and forces applied. The second area for evaluation is the space limitations which can be assessed by analyzing the range movement of a machine, the required installing space, the necessary space for routine maintenance, and the required space for machine interactions. The time limitation is the third area that involves the analyzing of the maintenance intervals for electrical, pneumatic, and mechanical components, lubrication intervals, fluid replenishment intervals, and tool life expectancy (Roudebush, 2005). Lastly, the assessor should evaluate interface limitations which involve analyzing the equipment’s interface with other equipment tools, energy sources, and auxiliary equipment.
Benefit from Our Service: Save 25% Along with the first order offer - 15% discount, you save extra 10% since we provide 300 words/page instead of 275 words/page
Identifying Machine and Task Hazard
Machine guarding risk assessment requires that all machines should be evaluated to determine if the machine poses significant situation hazard or a consequence task hazard. During the evaluation processes, an individual should consider all the life cycle stages of a machine tool including installation, commissioning, malfunction and correct operation, maintenance, and decommissioning (Roudebush, 2005). Typical equipment hazards that an individual should consider include shearing, part ejection, crushing, heat generation, entanglement, noise, nonionizing and ionizing radiation, the release of toxic mist and fumes. Whenever an equipment safeguarding depends on anything other than its intrinsic nature, the source of hazard should be determined during the risk assessment process. For example, a machine having an open belt drive poses an inherent danger.
Typical task hazards that risk assessor should be aware of include troubleshooting or trial run, setup, tool changing, loading and unloading, routine and unscheduled maintenance, recovery from crashes, product packaging, and major product overhaul. The one should also consider the intended use as well as the foreseeable misuse of the equipment.
VIP services
Extended revision period $2.00
SMS notification of the order status $3.00
Get order proofread by editor $3.66
Get order prepared by top 30 writers $4.40
Get a full PDF plagiarism report $5.99
Get VIP support $9.99
VIP SERVICES PACKAGE WITH 20% DISCOUNT $23.23
The development and establishment of an adequate machine guarding risk assessment involve gathering of information concerning how individuals interact with machines during all the phases of operation. Roudebush (2005) illustrates that to achieve this, the risk assessor can use the direct observation method. In cases where it is not possible, the evaluator may decide to conduct a simulated machine/human interaction. The data collected can be used to determine the extent of human exposure to machine hazards as a result of the interactions as well as the training experience required to operate a given machine. The individuals who could engage in the machine interaction task include maintenance personnel, machine operators, equipment installations, and removal millwrights, technicians, engineers, trainees, safety personnel, and supervisory personnel. The involvement of administrative staff is also necessary according to the parts they play in the procurement contracts of the machines.
Estimating the Risks
Evaluating risks involves developing a machine guarding risk matrix. There are different risk matrices; however, the assessor can produce distinct matrices for specific situations. The two primary categories of the machine risk assessment model include the probability of occurrence and the severity of harm. The severity of injury matrix considers the degree of damage and the extent of treatment medication. A catastrophic severity level is a permanent and disabling injury caused by machines (Parker et al., 2009). A serious severity level involves a disabling injury where a worker can continue to work. A moderate severity level involves a significant injury that requires treatment beyond first aid, and a minor injury involves a slight injury that requires first aid only. Probability occurrence levels consider factors such as workplace environment, the reliability of safety functions, human factors, and the awareness levels.
Try our Top 30 writers
Benefit from the incredible opportunity at a very reasonable price
Orderonly for $4.40
Determination of Risk Reduction Measures
Risk estimation helps by determining the level of risk, and allows the risk assessment team to develop parameters that they would use for risk estimation matrix. The one can eliminate hazards through machine design and machine guarding technologies. For example, an organization may opt to substitute the most hazardous substances with less hazardous materials, modify the physical features of the machine, and reduce the energy sources. Users and suppliers of the machines should share risk reduction responsibilities (Roudebush, 2005). The providers may decide to use international symbols as well as availing a series of different languages for the machines they supply.
Machine Guarding Risk Assessment Standards
There are different machine guarding standards and regulations with regards to risk assessment. They include Organizational Safety and Health Administration (OSHA) 1910.217 standards that specify the mandatory requirements for validation or certification of safety systems for security devices. ANSI B11.o-2010 standards provide the general rules and assessment of risk. ANSI/MMI B155.1 standards provide the requirements for safety when dealing with packaging machines. ANSI/RIA R15.06 standards provide the safety requirements when dealing with robot systems and industrial robots. ANSI/ASSE Z244.1 standards concern Hazardous Energy control and the alternative methods. ISO 12100-2010 provide the general principles for the design of machinery including risk assessment and reduction. Lastly, NFPA 79-2007 concerns the electrical standards for industrial machines. All these measures are interrelated.
Try our VIP support
Benefit from the incredible opportunity at a very reasonable price
Orderonly for $9.99
Conformance to the most current risk assessment standards may yield a lot of benefits for organizations. First, Manuele (2005) suggests that the current standards and consensus provide organizations with the greatest protection of workers from possible injuries and incidences. The consensus standards involve the state-of-art safety thinking on given topics. The latest standards are especially important because they contain experiences gained from using the previous standards as well as the advancements in technology (Sorano, 2005). Therefore, the most current consensus standards offer the most relevant solutions to contemporary machine safety situations and provide the strongest tools that organizations can use to prevent possible future injuries and incidents. Secondly, conforming to the latest machine guarding reduces enforcements concerns. Lastly, it reduces the level of liabilities for organizations.
Effective machine guarding risk assessment may also result in a host of other benefits including increased productivity and quality of products through improved controls such as sensors, tooling, and instruments software. Also, the effective risk assessment may lead to improved worker morale that can, in turn, result in a highly satisfied workforce. Moreover,the effective machine safeguarding risk assessment may improve the reputation of an organization and the owner of a machine due to the reduced levels of risk. Etherton (2007) illustrates that effective risk assessment may improve the efficiencies for designing and developing future machines and specifications as a result of a careful documentation of concepts, preferred approaches, and knowledge.
Affiliate Program: EARN 10%
from all orders made by people you bring!
Your people also get a 17% discount on their first order.
Conclusion
Machine guarding risk assessment is an important function of ensuring that the risk levels resulting from the use of the industrial machines are kept to tolerable levels. Risk analysis ensures the safety of workers, increases their motivation, and improves an organization’s productivity. Although this process is a complex one, it still can be compressed into five major steps. Those include gathering machine specifications and information, determining the machine limitations, identifying the task hazards and equipment hazards, estimating risks, and determining whether the level of risks is tolerable or not. A good risk assessment process must always ensure that the identified risks are reduced to a level tolerable by the national and international regulations and standards.
- Share this post with your friends: