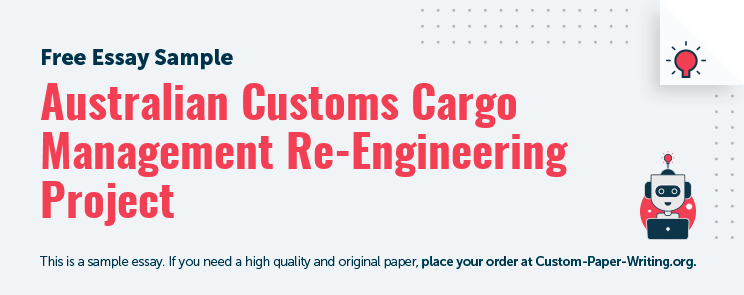
Introduction
Project management composes a dynamic process that uses the appropriate resources reasonably to achieve clearly identified targets. A significant part of projects experience failure, especially large-scale ones in public sector (Patanakul, P 2014). The case of failure leads to considerable losses both financial and time. Australian Customs Service is an organization, responsible for trade and travel regulation, profit collecting, and Australian laws’ implementation. The Customs core role is to carry the obligation to protect the community and to promote the legal cargo movement. A real practice case with Customs Cargo Management Re-engineering Project has proved that larger scope projects with many participants engaged results in much more challenging management.
Customs Service Project Background
In order to follow the fast-moving world, Customs noticed a necessity in updating. Cargo Management Strategy or CMS became the solution to modernize the cargo governance processes. It was targeted to unite processes, people, and technology, connected with cargo management. Later the CMS converted into the Cargo Management Re-Engineering Model aiming to improve the services’ delivery by reshaping the existing cargo mechanisms (Australian National Audit Office, 2007). Export processes, cargo management efficiency, and the high-risk cargo controlling were the major components of the Model.
Calculate the cost of essay
The project divided into several parts. The first one concerned the secure connection that enabled internal and external participants to act within the Interactive System and was called the Customs Connect Facility or CCF. The second was titled the Cargo Risk Assessment or CRA that, in its turn, identified and estimated conceivably high-risk cargo. Another element, called the Trade Modernization Legislation or TML, had to update the method of the cargo movement control and to establish the legal basis for the electronic business environment.
Owing to the project’s scope and careless planning, the CMR experienced delays and substantial cost increases. Thus, Australian Customs spent approximately $225 million on modernization the cargo system, instead of planned $30 million, which necessitated a great need for investment (Australian National Audit Office, 2007). In fact, the comparison of the work expenditures against benefits was a difficult task.
Stakeholders Involved
For successful running, the project lacked an effective structure which would direct and manage it or make certain responsible decisions. For this task, Customs has had almost 10 bodies managing different project elements. These bodies intersected in their responsibilities, but the project did not have a single leader. Thus, accountabilities for its delivery were unclear as well as responsibilities division and project targets (The Infonomics, 2006).
Limited time Offer
with code
The Industry Reference Group or IRG and the Industry Working Group on Customs or IWGC were started as two key industry forums in March 1999 (Australian National Audit Office, 2007). The IRG was dealing with strategic industry approach to the CMR project. In its turn, IMGC aimed to rationalize and coordinate consulting arrangements instead of forming the Customs Cargo Consultative Committee.
The Electronic Data Systems or EDS decided to join the applications’ development task fulfillment. In 1998 under Customs outsourcing arrangements EDS began to generate the applications for the project. In October 2001 Customs and EDS reached an agreement that EDS undertakes the interface, desktop, and special options of the project. One or more third sides would deal with the analytical and development aspects. At the beginning of 2002, the ICS building involved the Computer Associated Consortium. To develop the CCF, managers signed separate contracts with IBM and SecureNet (Australian National Audit Office, 2007). Taking into account the scale of the project, the deadline pressure upon Customs was significant.
Benefit from Our Service: Save 25% Along with the first order offer - 15% discount, you save extra 10% since we provide 300 words/page instead of 275 words/page
Project Implementation
The project realization contained three releases. In March and April 2003, the first release considered completing the test with the industry. The second release, that took place on 6 October 2004, concerned the export component. The third one was implemented on 12 October 2005 regarding processing of imports (Australian National Audit Office, 2007).
By approaching the end of 2003, the scheduled time terminated and the project faced delays and cost overruns. The assumed budget increased the amount to $100 million as well as deadlines were postponed to 2004. Cost of the project had risen to $250 million by the 2005. Reports regarding problems did not appear until the project was launched on 12 October 2005. The Customs was confident that the situation was under control and the system would be implemented at the Christmas import period (Australian National Audit Office, 2007).
Comparing to imports, exports realization appeared to be less complex and had fewer industry participants. In contrast, import part significantly influenced the supply chain and international trade of Australia. There were also problems with CCF and ICS operating. The substantial disruption occurred to the cargo movement, particularly in the sea environment. According to reports, during several weeks Australia’s main ports were overloaded with accumulated containers awaiting clearance and delivery (Australian National Audit Office, 2007). Thus, lack of the thoroughly considered plan resulted in undertaking decisions in a crisis environment. The reason of this unfortunate situation was also in poor project management and poor estimation of the work scope. In addition, there were too many stakeholders, among which there was no sole responsible project manager. As a result, too little consultations and exacerbation of problems instead of their resolving resulted in project’s failure.
VIP services
Extended revision period $2.00
SMS notification of the order status $3.00
Get order proofread by editor $3.66
Get order prepared by top 30 writers $4.40
Get a full PDF plagiarism report $5.99
Get VIP support $9.99
VIP SERVICES PACKAGE WITH 20% DISCOUNT $23.23
Many Customs’ operators faced the difficulties while dealing with their third-party software and attempted to use the ICS via online Customs Interactive means. This endeavor also failed because of poor usability of the system and its slow performance due to the fact that there were numerous users during that time. The industry tried to respond to these issues through the Customs Help Desk. It also could not handle so much traffic and, therefore, was unable to manage all the requests. This reflected that managers considered appropriately neither support requirements nor technical issues (The Infonomics, 2006).
Furthermore, several changes in the system led to severe disruptions and resulted in huge manual work-around, which, in its turn, reduced the process efficiency. Successful project features lay in more careful project planning, meeting objectives of time, numerous technical and business aspects (Young, 2013). Careful planning is essential to execute the project targets in the correct order and to be confident that they meet deadlines minimizing waiting time and resulting in cost overruns.
Try our Top 30 writers
Benefit from the incredible opportunity at a very reasonable price
Orderonly for $4.40
Factors of Project Failure
Due to numerous threats, it was obvious that the project needed ongoing, high-level focus to ensure it went smoothly. However, numerous challenges, especially regarding imports release, took place. Underlying the roots of problems, one can spot several causes of such a failure. The first among them is an inappropriate cross testing of the system. Proper testing with live data would have defined numerous weaknesses of the system and assisted their advance liquidation. The second issue concerns the quality of third-party software. It was inconvenient to communicate within the Customs through the system. In turn, software providers faced difficulties in creating, testing, and releasing product in time to meet Customs’ short deadlines (Booz Allen Hamilton, 2006). Additionally, inadequate training added cons to project planning. Without staff appropriate training, organizations were not ready to adapt their own processes to the certain requirements of the new system.
Try our VIP support
Benefit from the incredible opportunity at a very reasonable price
Orderonly for $9.99
All these aspects stemmed from the lack of phased implementation. Chaotic steps realization leads to falling back when any problem arises. Thus, there were many unrelated flaws in the system implementation process from the very beginning. One of the most significant was that Customs undertook the responsibilities only within its boundaries department. It is rather important, as changes covered the entire industry with Customs acting as a central governing agency. To improve the efficiency of industry operation it had to manage changes across the entire industry.
Finally, no one was totally responsible for the actions. Misunderstanding between the partners arose due to multiple participants. This way, a poor management structure influenced a variety of project activities including costs, schedule, and unclear project targets. The underestimating of the abilities to implement a rather complex system in such a short time and the lack of understanding of this mechanism could be also mentioned as one more reason for the project failure. The system operated on multiple platforms, which influenced on its integration due to the complexity, resulting in inadequate requirements for the project.
Affiliate Program: EARN 10%
from all orders made by people you bring!
Your people also get a 17% discount on their first order.
Lessons to Learn
Therefore, this project has been one of the most dramatic failures in Australia’s public sector. The managers continually postponed the deadline, constantly expanded the budget, and neglected periodically made warnings. As a result, it has become a serious trial for Customs to generate and complete a project of such scale and complexity. Taking all the factors into account the following causes could be highlighted: poor defining of objectives at the beginning, inadequate schedule management, weak leadership, lack of senior management commitment, poor planning and control, no effective communication process, assumed knowledge, skills of team members, not clear scope, confused roles and responsibilities.
Thus, the project management lacked many basic essential ingredients vital for successful implementation. Such an experience should serve as a significant scope of lessons for managers of different companies regardless of their level. Firstly, in order to escape the similar situation, a project should be managed by one responsible leader, who would direct all the actions and consider all the stakeholders’ interests. Secondly, there should be clearly defined outcomes and benefits of the project managers want to reach. The project planning, identifying the project needs, financial and budget valuation, and appropriate risks estimation are highly essential to avoid failure. Finally, quick response to emerging issues and changes during project’s implementation should help avoid underestimation of possible risks and carefully consider technical issues.
- Share this post with your friends: